As part of an ongoing goal to reduce greenhouse gas emissions and limit the impact of global warming, electric vehicles (EVs) are being widely adopted globally. To date, more than 20 countries have announced plans toward electrification goals or banning of traditional internal combustion engine (ICE) cars by no later than 2050, and more than 120 countries and the European Union have announced net-zero pledges in the coming decades.
Moreover, car companies are beginning to aggressively pursue the electrification of their respective fleets; Mercedes-Benz has announced that it will electrify its entire future lineup by 2030; Audi has declared that it will abandon the manufacture of all ICEs entirely by 2033 while launching only all-electric vehicles by 2026; Ford, General Motors (GM), and Stellantis intend to ensure that 40%–50% of their sales are for zero-emission vehicles by 2030; and Volvo is going to replace its entire lineup with all-electric cars by 2030. With such aggressive growth of EV production, the demand for battery-related raw materials, like Ni, Co, Mn, Li, and graphite, has naturally led to an increase in mining and production. However, even at the current level, there would be a long lead time to meet the expected demand of the global supply chain.As a result, it is predicted that there will be a severe shortage of raw materials in the future, especially for Li and Co.
Meanwhile, because the average lifespan of LIBs is 1–3 years for consumer electronics and 8–10 years for EVs or energy storage systems,approximately 0.2 million tons of spent consumer LIBs and 0.88 million tons of spent power LIBs will be generated by 2023. If the spent LIBs cannot be adequately handled, the considerable amount of spent LIBs will create significant environmental concerns, particularly as toxic heavy metals and gases, such as Co, Ni, Mn, and HF, could be released into the environment from improperly handled spent LIBs.
Large accumulations of spent LIBs combined with improper handling can also pose as a significant fire and explosion hazard.5 However, spent LIBs can also be viewed as a resource. The internal materials in spent LIBs are all battery-grade, so they can be reintroduced into the production of new batteries. Therefore, the recycling of spent LIBs could provide a secondary source of materials generation to feed into the supply chain for new battery manufacturing.
Furthermore, employing recovered cathode materials could save over 20% of the total cost of a LIB, and more potential savings can be realized by recycling more components beyond cathode materials from spent LIBs.6 In summary, LIB recycling can play a critical role in alleviating the current and future supply chain concerns, prevent possible pollution and environmental hazards, and generate sustainable and continuous economic benefits. It is a key piece of the puzzle toward the realization of sustainable LIB development for a greener society. In this paper, we will discuss both the technical and business challenges of LIB recycling, which is shown below.
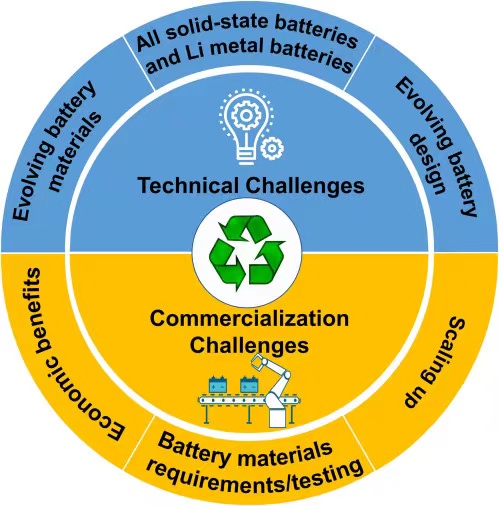